Introduction to Turbine Engines
- Krish Pesswani
- Jan 15
- 4 min read
Updated: Apr 2
Today on AeroIntellect, we will dive deep into the different types of turbine engines and look over their operating principles, design features, pros, cons, and applications.
So, what is a turbine engine? A turbine engine is a type of jet engine used in our typical passenger aircraft and fighter jets. The three most common types of turbine engines are turbojet engines, turboprop engines, and turbofan engines, each having its own unique feature. However, the turbine engines are based on the same basic design: Air intake.
Air Intake, also known as air inlet, functions as the engine's "mouth" and is responsible for generating thrust in an aircraft. It ensures that the jet engine gets a steady and controlled

supply of air in order to support the combustion process and maintain the proper pressure
and flow conditions for efficient engine operation. In jet engines, air is taken in, compressed, mixed with fuel, ignited, and expelled at high velocity, producing thrust.
Even though this concept is common in all jet engines, each has its distinctive design, enabling it to have different applications.
Turbojet Engine
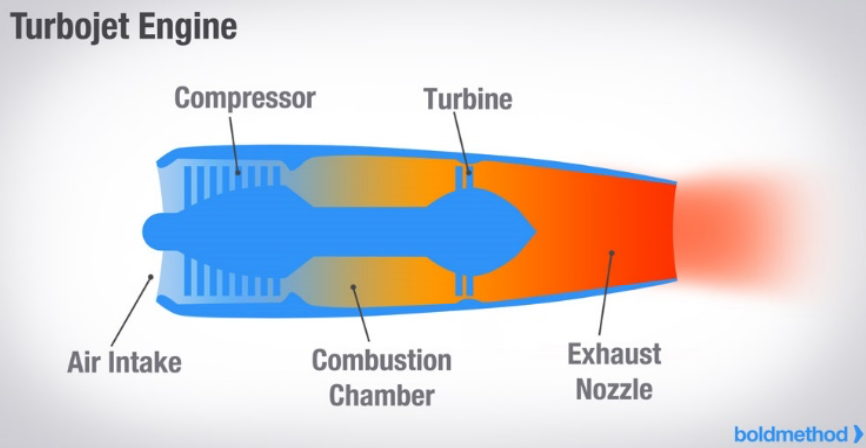
Turbojet engines are the simplest form of jet engines optimized for high-speed performance. They are used in supersonic jets (jets traveling faster than the speed of sound) and military aircraft, such as Concorde. The main components of a turbojet are:

Compressor: As the air enters the system, it is compressed, increasing the temperature and pressure. The pressure is increased for fuel to burn efficiently; high pressure improves the mixing of fuel and air, enabling better combustion. As shown in the thermodynamic principle (ideal gas law), compressing the air reduces its volume (V), increasing its pressure (P). The temperature is increased as air with a higher kinetic energy ignites fuel more quickly in the combustion chamber.
Combustion chamber: Fuel is injected and burned in the compressed air, creating high energy exhaust gas.
Turbine: The expanding gas passes through a turbine, which powers the compressor at the front of the engine.
Exhaust nozzle: The high-velocity exhaust gases are expelled through the nozzle, producing thrust.
As mentioned before, turbojets are very efficient at supersonic speeds, this is because they are designed to expel gases at extremely high speeds. However, at subsonic speeds (slower than the speed of sound), they are very inefficient as they generate more noise and burn more fuel.
Turbofan Engine
Turbofan engines are the most common type of jet engine used in commercial aviation today. Turbofan engines are an evolution of the turbojet, designed to be more efficient at subsonic speed.
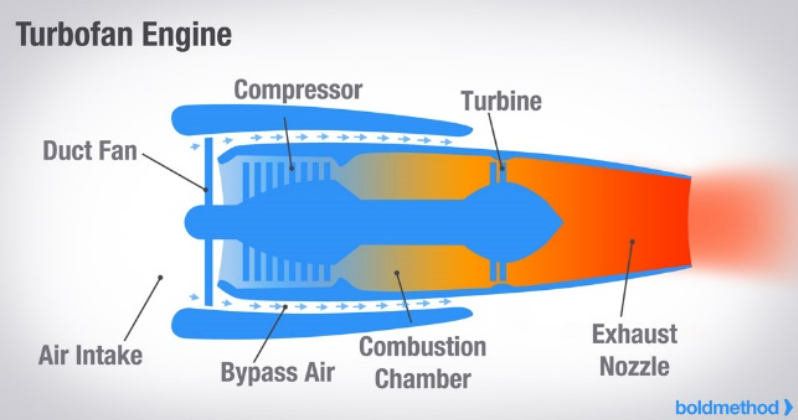
The difference between a turbojet and a turbofan is obviously the size and the large fan located at the front of the engine responsible for pulling much more air in and contributing to noise reduction, which is crucial in aviation requirements. You must have noticed something new in the diagram: the bypass air; this is when the air goes over and under the engine's core and is accelerated by the fan. The ratio of air bypassing the engine core to the air going through the combustion process is known as the bypass ratio.
Low-bypass turbofans: These types of engines consist of a relatively small fan passing most of the air through the engine core. They are used chiefly in the military or business jets.
High-bypass turbofans: These engines have a much larger fan with most of the air bypassing the engine's core instead of entering in it, making it more efficient at lower speeds, such as take-off and landing. A320 and B737 are both common examples of aircraft powered by high-bypass turbofans.
However, turbofans do have some limitations: due to more components, the maintenance requirements increase, they are inefficient at supersonic speed, and they have a higher weight.
Turboprop Engine

Turboprop engines share similar components as a turbojet engine – a compressor, combustion chamber, and turbine – although, unlike turbojet, the turbine in a turboprop is not only responsible for driving the compressor, but it is also accountable for extracting energy to power the propeller shaft through a reduction gearbox, and not to produce thrust directly from exhaust gases. In short, this means that the propellor generates most of the thrust generated by the turboprop engine.
Turboprop engines are highly efficient at lower speeds and lower altitudes (under 450mph and below 30,000 feet), giving them an excellent ability to take off and land. They do not excel at high speeds because the propeller becomes less efficient as airspeed increases. They are used in fields where fuel efficiency and operating cost are more important than speed, such as surveillance planes.
In conclusion, the turbojet, turbofan, and turboprop engines represent distinct technological advancements tailored to specific aviation needs. The turbojet, the earliest jet engine, excels at high speeds and altitudes, making it suitable for supersonic and military applications. The turbofan, with its high bypass ratio, balances thrust, fuel efficiency, and noise reduction, dominating commercial aviation and subsonic long-haul flights. Finally, the turboprop engine combines the benefits of a gas turbine with the propeller's efficiency, excelling in short-haul, low-speed, and rugged operations.
Thanks for soaring with me through the intricacies of propulsion systems! Join me next week as we explore another fascinating facet of aerospace innovation.
Comentários